From Layout to End Up: The Complete Light Weight Aluminum Casting Process Demystified
In the world of manufacturing, the procedure of light weight aluminum spreading stands as a crucial approach that has actually fueled markets for decades. Each step in this elaborate process, from the preliminary layout phase to the last complements, plays an important role in shaping the outcome of the item. Nonetheless, what absolutely exists beneath the surface of this procedure remains a secret to several. By unraveling the intricacies and clarifying the subtleties entailed in each phase, a deeper understanding of the art and science behind light weight aluminum spreading emerges. about aluminum casting. Stay tuned as we study the full light weight aluminum casting procedure, discovering the details that change resources into refined products.
Designing the Casting Mold
When starting the light weight aluminum casting procedure, thorough attention to developing the casting mold and mildew is vital for guaranteeing the end product's honesty and high quality. The casting mold works as the structure for the entire casting procedure, dictating the shape, dimensions, and surface coating of the eventual aluminum part.
To develop a reliable casting mold and mildew, designers should take into consideration numerous variables such as the intricacy of the part, the kind of light weight aluminum alloy being used, and the preferred residential or commercial properties of the last item. about aluminum casting. Computer-aided design (CAD) software application is often employed to develop in-depth schematics of the mold, permitting precise customization and optimization
In addition, the layout of the casting mold and mildew straight affects the performance and cost-effectiveness of the spreading process. A well-designed mold and mildew decreases material waste, reduces the need for extensive post-casting machining, and enhances overall production rate.
Melting and Putting Light Weight Aluminum
With the style of the spreading mold and mildew completed, the next critical action in the aluminum spreading procedure is the melting and putting of the aluminum alloy. The procedure begins with filling the aluminum alloy right into a heating system where it is warmed to its melting factor, generally around 660 ° C(1220 ° F) for light weight aluminum. Crucible heating systems, induction heating systems, or gas-fired reverberatory heating systems are typically utilized for melting aluminum. Once the light weight aluminum is liquified, it is important to maintain the temperature level within a specific array to make sure the quality of the spreadings.
The molten aluminum is carefully moved from the heating system to the casting mold. Appropriate putting methods contribute substantially to the general quality of the final aluminum casting.
Cooling and solidifying Process
Upon completion of the putting process, the molten aluminum shifts into the cooling down and solidifying stage, a critical point in the aluminum casting procedure that straight impacts the final product's integrity and features. As the aluminum begins to cool, its molecules prepare themselves right into a solid form, gradually handling the shape of the mold. The rate at which the aluminum cools is critical, as it affects the material's microstructure and mechanical residential properties. Quick cooling can result in a finer grain structure, improving the material's strength, while slower air conditioning may lead to bigger grain sizes, influencing the last product's ductility.
During this phase, it is important to manage the cooling procedure thoroughly to stay clear of issues such as porosity, contraction, or internal anxieties. Numerous air conditioning approaches, such as air cooling, water quenching, or controlled cooling chambers, can be utilized based on the certain needs of the spreading (about aluminum casting). By keeping track of and managing the solidification and cooling process, makers can guarantee the production of high-grade light weight aluminum castings with the desired metallurgical and mechanical residential or commercial properties
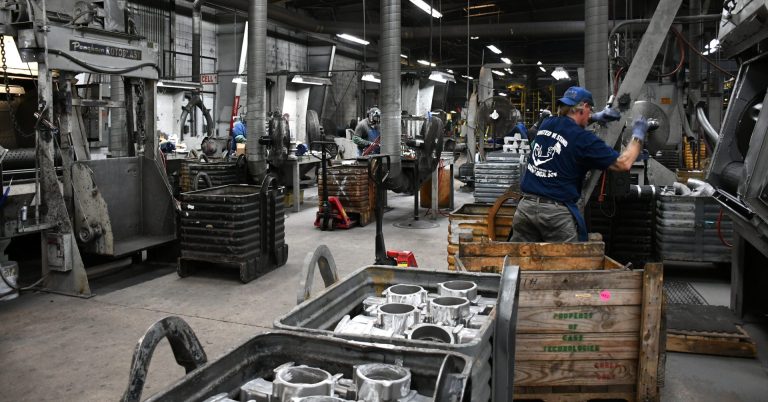
Getting Rid Of the Final Casting
Once the light weight aluminum spreading has adequately strengthened and cooled in the mold, the next action in the process includes carefully getting rid of the final casting. This step is critical to make sure that the light weight aluminum part is successfully extracted without any damages or issues.
To remove the casting, the mold and mildew is opened up, and the casting is removed using numerous approaches relying on the complexity of the mold and the part style. For easier forms, the spreading can usually be quickly eliminated by hand or with simple devices. For more complex layouts, added tools such as ejector pins, air blasts, or hydraulic systems might be needed to facilitate the elimination process without triggering any damage to the spreading.
After the casting is efficiently eliminated from the mold and mildew, any kind of excess product such as gates, runners, or risers that were utilized throughout the casting process are trimmed off. This action aids in accomplishing the last desired shape of the aluminum part prior to it undergoes any type of additional finishing processes.
Finishing and Top Quality Evaluation
The final phase in the light weight aluminum casting process entails meticulous completing methods and extensive high quality inspection methods to guarantee the stability and precision my response of the actors light weight aluminum parts. Ending up techniques such as grinding, fining sand, and shot blasting are utilized to get rid of any kind of excess material, smooth rough surface areas, and improve the aesthetic allure of the final item. These procedures not just enhance the look however likewise guarantee that the components satisfy the specified dimensional tolerances and surface area coating needs.
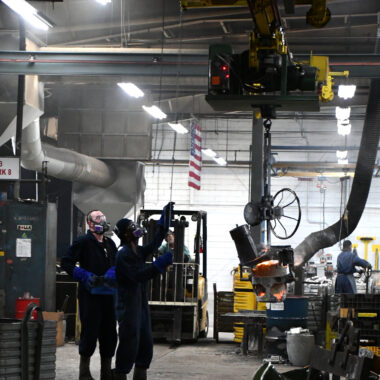
Verdict
Finally, the aluminum spreading procedure entails making the mold, melting and putting aluminum, strengthening and cooling down the spreading, eliminating the end product, and do with a quality inspection. Each step is critical in making certain the last item satisfies the preferred requirements. By understanding the entire process, manufacturers can generate high-quality light weight aluminum castings efficiently and effectively.
Stay tuned as we dissect the total aluminum casting process, revealing the ins and outs that transform raw products into refined products.
With the layout of the spreading mold wrapped up, the next important step in the aluminum casting procedure is the melting and pouring of the light weight aluminum alloy.Upon completion of the putting procedure, the molten aluminum transitions right into the strengthening and cooling phase, a crucial phase in the light Our site weight aluminum casting process that directly affects the last item's stability and attributes.The last phase in the aluminum spreading procedure involves thorough ending up strategies and rigorous quality inspection protocols to make certain the stability and precision of the actors light weight aluminum components.In final thought, click for more info the light weight aluminum spreading process includes creating the mold and mildew, melting and putting aluminum, solidifying and cooling down the casting, getting rid of the last product, and completing with a high quality inspection.